Here is part seven of our series "Digitalisation 2021". In the other articles, we looked at digitalisation in sales, IT security, marketing, logistics, finance, procurement and controlling. This article is about digitalisation in manufacturing. Note: This article does not distinguish between production and manufacturing, i.e. when we talk about production, we also mean manufacturing.
Digital transformation of production is changing everything: workflows, processes, energy consumption of factories and manufacturing plants, labour behaviour, sustainability as well as the entire supply chain. And not only that. It is also changing the way products are designed, manufactured, used and shipped. That' s pioneering. That's groundbreaking. THAT is a real transformation.
All this is achieved through the „smart factory", the (Industrial) Internet of Things (IIot/IOT), digital twins, sensors and other technologies that are part of Industry 4.0 / I4.0. You can find a detailed article explaining Industry 4.0 with its technologies here. We will come back to the digital twin later in this article.
"The term Industry 4.0 refers to the result of the fourth industrial revolution. The fourth industrial revolution is characterized by a combination of automated, traditional manufacturing and industrial processes with intelligent technology and machines that communicate with each other independently."
And the figures speak for themselves. According to the Boston Consulting Group, Industry 4.0 will add 1 per cent to Germany's gross domestic product (GDP) until 2025 and create 390,000 jobs (GDP Germany in 2020: 3.33 trillion euros). Deutsche Bank also estimates similar figures, 267 billion for the period 2015-2025.
What is digitalisation in production?
When it comes to digitising production, the digital interconnection of machines, processes, data, departments, suppliers, partners and customers is the essential element in this transformation. Otherwise, as with every digitisation, data must be digitally captured, structured and merged. In the process, huge amounts of data are generated (Big Data), which in turn can be used, for example, to make processes more efficient, to maintain machines, to make forecasts or to develop new business models (see Fig. 1).
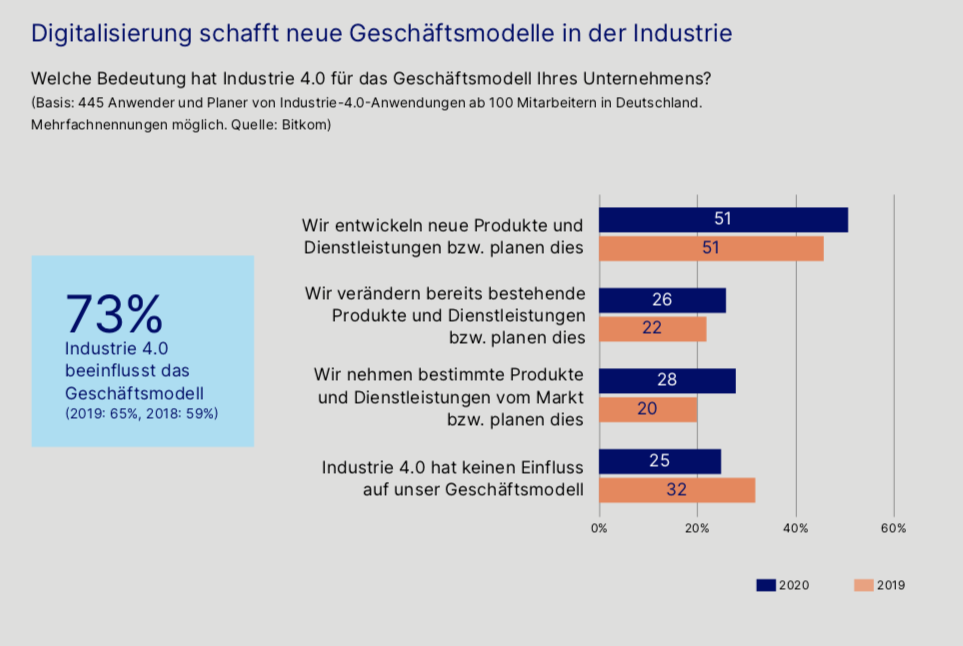
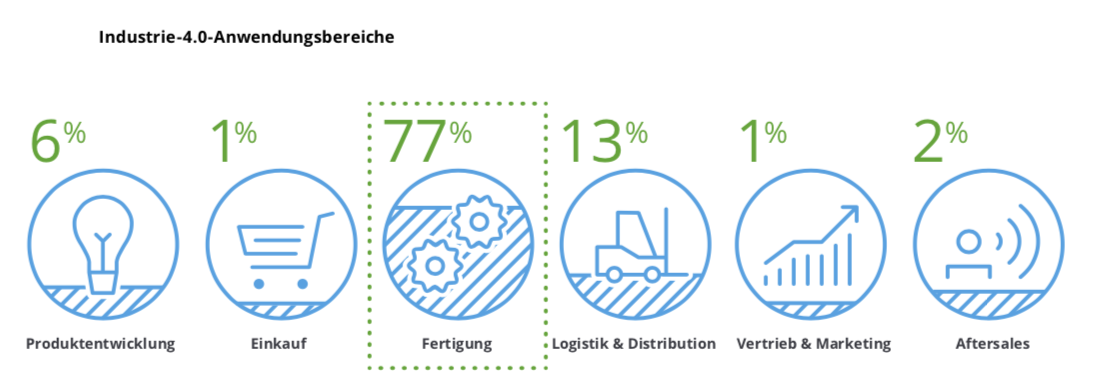
And precisely this comprehensive digitalisation of industrial production falls under the term Industry 4.0 (also called Manufacturing 4.0 or M4.0), which we will now use from now on as a synonym for the transformation in this area. The smart factory is at the centre of Industry 4.0, as the following figure shows (Fig. 3). Great importance is also attached here to the supply chain, and the combination of the digital supply chain with the smart factory generates maximum efficiency and effectiveness.
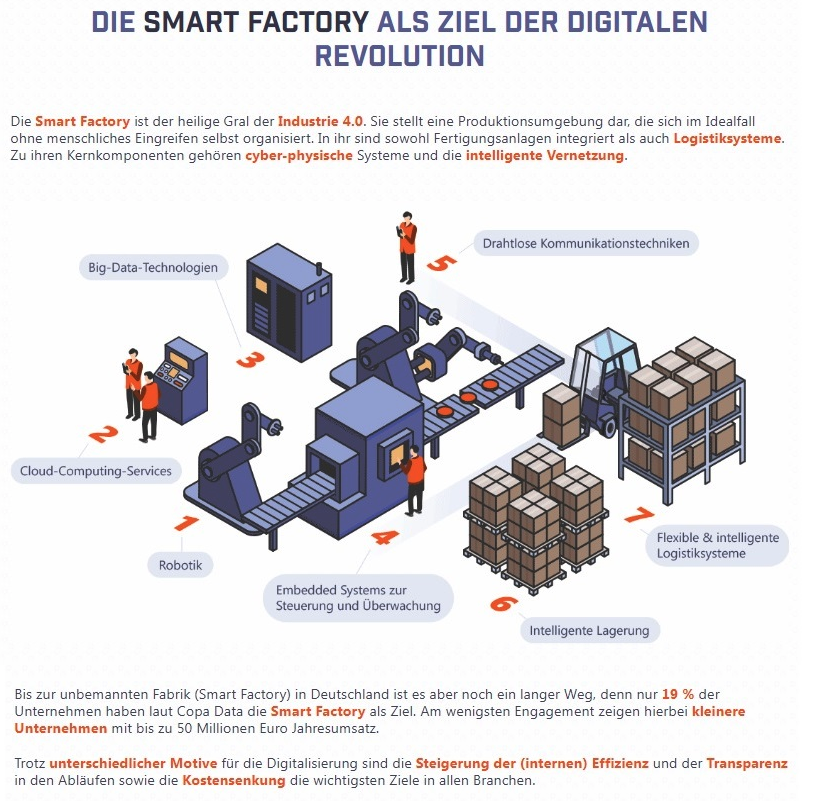
The four steps of digitalisation in production
The path towards the smart factory can be realised in four steps:
Networking
As already mentioned, interconnection is the basis on which digitalisation is built. Systems, machines and plants can be networked using IoT technologies. Data can be collected with the help of sensors. This means that either new systems are procured or old systems are upgraded (so-called "retrofitting").
Analysis
With the aid of graphical reporting systems (e.g. dashboards), the data collected provides the necessary transparency and can also be used for monitoring purposes. The data does not only come from the smart factory - information from procurement, sales, quality analysis and the company's own ERP (Enterprise Resource Planning), which is increasingly becoming the central hub for digital processes (see here under "Cloud ERP and democratisation"), converge here. This provides the basis for any optimisation and shows which processes and workflows can be improved or where critical vulnerabilities are lurking in production.
Optimisation
Systems are networked, data flows together and the analysis provides important findings and insights for optimisation. Everybody is talking about "predictive maintenance" - now you are also in a position to use this scenario. Other possibilities are the effective management of peak loads and the optimisation of manufacturing processes up to a self-controlling production.
Smart Services
From this point on, a company is ready for the final step in digitalisation: data-based business models and smart services - this is where additional value is created for customers as well as creating new revenue potential and sales markets for the provider. Thanks to the data that has provided optimisation in the previous step, new business models can also be derived. Often these data-based services run as "as-a-service", such as Microsoft Office 365, which is sold as "SaaS" (Software-as-a-Service). Instead of a one-time licence, usage is billed over time.
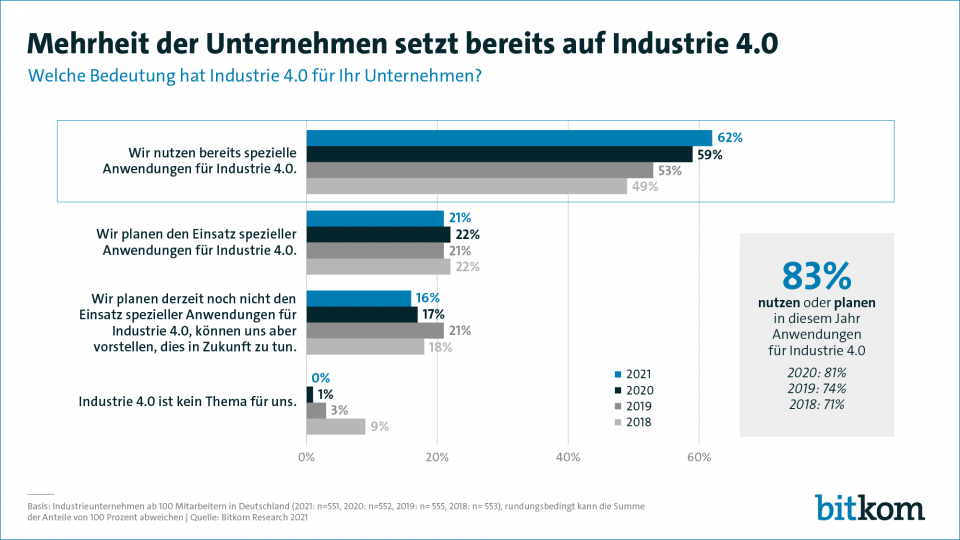
Opportunities, obstacles and risks
According to a recent Bitkom survey (April 2021), 95 percent consider Industry 4.0 an opportunity for their own company, only 4 percent see it as a risk. But we are far from fully exploiting the corresponding opportunities:
"Not even one in three industrial companies in Germany (31 percent) currently sees itself as a pioneer in Industry 4.0. More than one in two (54 percent), describes itself as a laggard, and one in nine (11 percent) even thinks it has missed the boat."
Bitkom
So why is that?
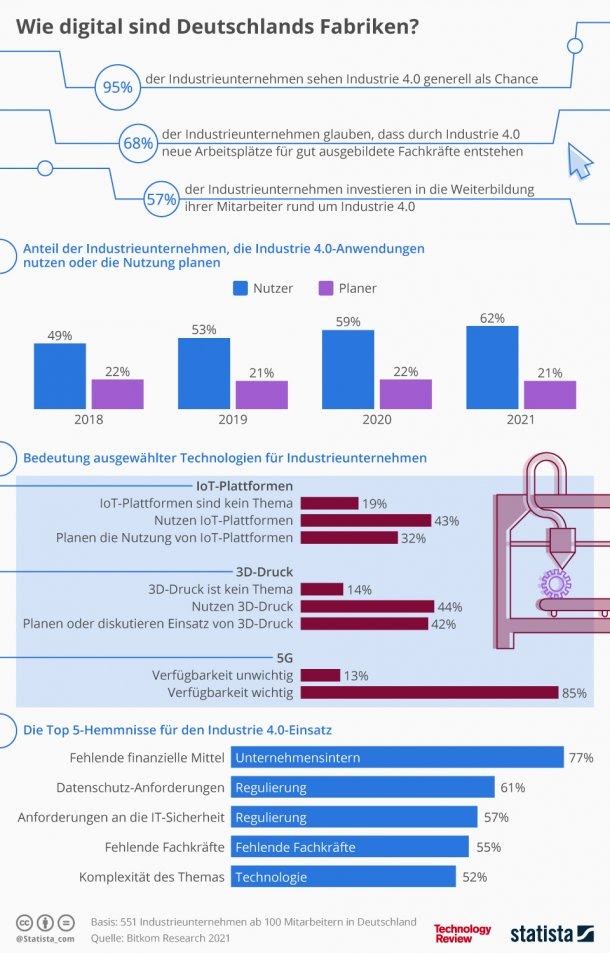
Obstacles
Lack of financial resources is by far the most significant factor, as can be seen in the bottom part of Fig. 5. Some 61 % feel thwarted by data protection requirements, closely followed by IT security requirements. These are high and complex in Industry 4.0 - read our article "Digitalisation of IT security".
The shortage of qualified staff at the fourth position is a problem that is common to all industries (55 %). And without the appropriate specialists, it becomes difficult to decipher the complexity of the subject - a good half of all respondents (52 %) complain about this problem.
One more aspect not listed here is the fear of digitalisation itself and its internal resistance. Production employees in particular (see Fig.6) are worried about their jobs, and this fear is not without justification. Digitalisation is also a cultural change in general, which often encounters a reluctance to change. Companies need to initiate this cultural change appropriately, address justified and unjustified concerns and problems and properly prepare their employees.
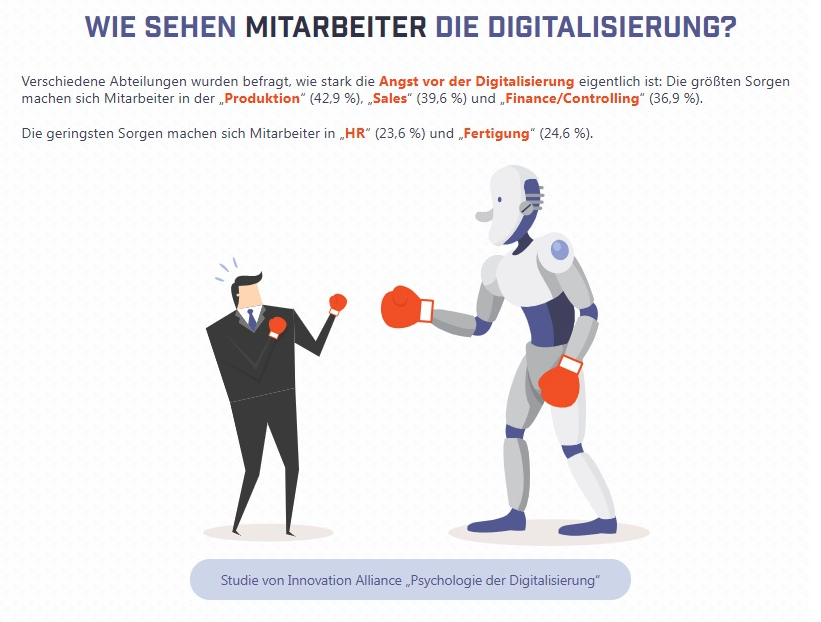
Risks
And as if the obstacles were not enough, there are also certain risks to be taken. We have already mentioned the security aspect - the interconnectedness of the individual areas increases both the surface for attack and the number of possibilities to penetrate a system. Another problem is that technology standards have not yet been established, especially in the area of sensors. And then there is the danger of setting the wrong priorities due to a lack of knowledge and experience and, in the worst case, no longer being competitive.
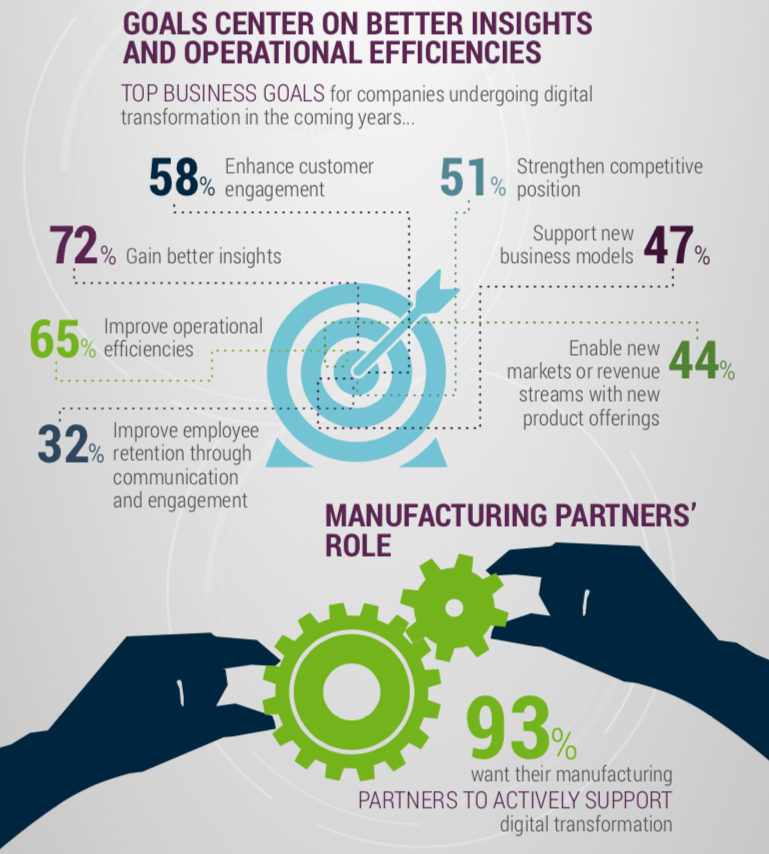
Opportunities and objectives
On the flip side, there are opportunities ahead, which is why most companies have the following goals (see Fig. 7, survey of over 300 production and manufacturing specialists): powerful connected systems enable deeper insights that can be used to make better business decisions (72 %). These insights also enable optimisation in terms of process and sequence efficiency (65%). Furthermore, customer engagement can be increased, partly due to a better customer relationship (58 %). Not only does the relationship with the customer improve, but the relationship with partners and suppliers also becomes more trusting if the company opens up to them in the course of digitalisation. Besides strengthening their own position in competition (51%), companies hope for new business models mentioned at the beginning (47%), which in turn can be found in the deeper insights - or not.
Industry 4.0 and the smart factory
We are now familiar with Industry 4.0 as a synonym for digitalisation in production. Smart factories are characterised by their intelligent networking (read the example of a smart clothing factory here).
"Due to our technological progress, machines can now independently record information, interpret it and communicate with each other."
In order for equipment and machines to be able to communicate, a so-called "digital twin" is created in addition by connecting them to the network.
Digital twin
Put simply, a digital twin is a digital replication of a mostly physical object, process or system. However, this object does not necessarily have to exist in the real world - digital twins are often created in the conceptual phase to simulate future objects such as machines or systems in advance. In addition, they allow for the cross-sectoral exchange of data in the form of intelligent networking.
Smart factory workforce
The final piece of the puzzle in a smart factory is the workforce. In manufacturing and other industrial sectors, 80% of the workforce is "deskless". These employees will be equipped with digital tools that transform them into a "networked employee". This makes paper-based data a thing of the past - a quantum leap in terms of efficiency, productivity and also quality assurance.
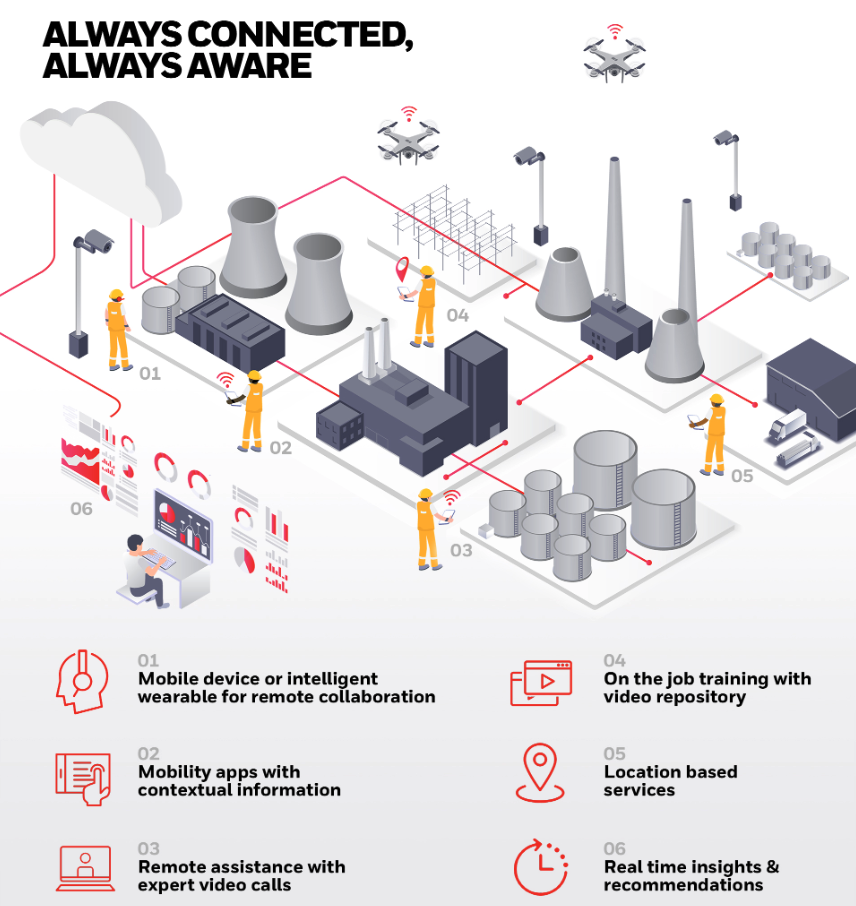
The future of digital manufacturing
As a result of the strengthened relationship with the customer, their feedback will have a more significant impact on the production process in the future. This includes customised and one-off products ("batch of 1"), smaller order quantities and shorter delivery times. Amazon already offers "same day delivery", i.e. delivering on the evening of the order day.
In addition, manufacturers are also trying to optimise product development and the design process (also called the "engineering chain“). With so-called "front-loading", the identification and resolution of problems are shifted into the early phases of the product development process. The previously mentioned digital twins make it possible to link the separated areas of engineering chain, supply chain and service and maintenance. These different network infrastructures can be visualised as schematic representations including all relevant information about infrastructure, resources and capacities as well as the dependencies and relationships between them.
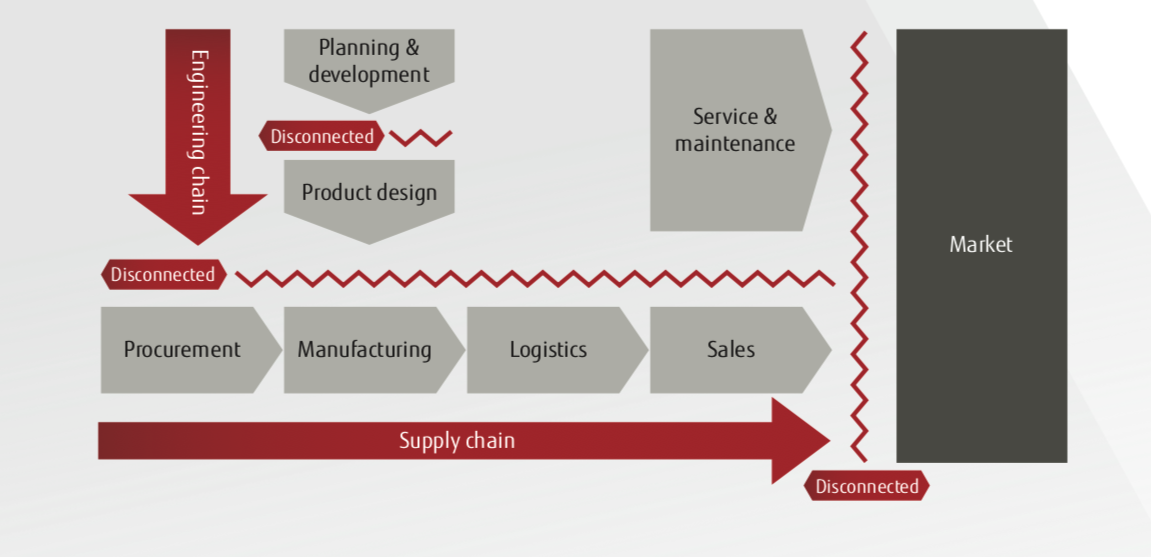
It becomes apparent once more that networking the internal systems alone is not enough. Substantial added value is created when manufacturers, suppliers, partners and customers become part of a networked ecosystem. In the previous article on the digitalisation of procurement, we already talked about the relationship between all participants in the supply chain that creates equal value. In addition to the benefits, such relationships also create greater resilience, which has been underlined by recent crises such as Covid-19.
Production based on experience
In order to be even closer to customers and their wishes, digitalisation creates a stronger bond between production and customers. More and more companies are using a subscription based model, where customers have continuous access to products or services and pay for this period of time. Some examples are Spotify, Netflix, Amazon Prime or HelloFresh. The benefit of this model is, on the one hand, the ongoing revenue and cash flow. Yet more importantly, companies become better acquainted with the customer and can collect data on a continuous basis. This enables them to create better products and services that are even more in touch with the customer.
Software-based production
The desire for physical products has been radically changed by digital applications, solutions and services. MP3s have replaced the CDs and records of this world, and Spotify is replacing the desire to buy and own any of these media. The same trend can be observed among manufacturers - in the past, only the equipment was delivered, nowadays software-based services are provided for the operation of these equipment or, if necessary, the software completely replaces the equipment.
Moreover, the above-mentioned relationship, which is equally value-adding for a rapidly changing market, may provide for the development of other new business models. For this purpose, companies need to collaborate with other companies, start-ups, partners or research institutions. And this can also be done with software support through standardised interfaces (so-called APIs).
Changing role of people in production
The high level automation and digitalisation in the course of smart factories is reducing the number of factory employees. The remaining employees also work in a new way, as we have described before. Furthermore, requirements are also shifting - specialised employees are needed who are able to cope with the digital challenges of Industry 4.0, as well as data scientists who can evaluate the mass of digital data and use it profitably. Not to mention the IoT professionals who lay the foundation for smart networking and turn every factory into a smart factory.
Conclusion
Of all the digital transformations, the upheaval in production seems to be the most exciting. The completely automated factory in the sense of a smart factory is the fulfilment of a millennia-old dream of humankind.
However, here too there are some challenges to be circumnavigated - if you don't plan carefully, have your staff support your mission, and acquire the required expertise in the form of knowledge and the relevant experts, you run the risk of landing in a costly dead end. And, as always, the bigger picture must be understood so that different technologies, solutions and approaches fully merge into a holistic strategy plus synergy and the whole becomes far more than the sum of the parts. Start small, but plan big.
Or in the words of Deloitte: Think Big. Start Small. Act Fast.